Технология регенерации: повышение эффективности использования топлива, необходимого для работы системы дозирования
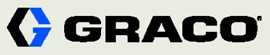
Интегрированные системы дозирования Graco® Reactor™ (рис.1 и 2), используемые для подачи пенополиуретана или полимочевины включают в себя дозатор и дизель-генератор. Это первое в своем роде оборудование, использующее технологию регенерации для улучшения качества распыления и сокращения расхода дизельного топлива.
Идея создания новой интегрированной системы возникла в результате
возросшей потребности в использовании более компактных и экономичных
систем дозирования. Было необходимо создать недорогую в обслуживании систему,
которая смогла бы обеспечить необходимый уровень качества
и производительности, обладая при этом невысокой стоимостью.
Используя технологию регенерации в конструкции новой системы, инженеры компании Graco, поставили перед собой три основные задачи:
-
разработать полноценную, портативную, топливосберегающую систему;
-
оздать удобную систему управления и интуитивно понятный пользовательский интерфейс;
-
улучшить или обеспечить ранее достигнутый уровень производительности.
Регенерация – процесс совместной выработки электрической и тепловой энергии. В конструкции новой интегрированной системы применяется двойной контур охлаждения, что позволяет использовать тепловую энергию, получаемую от системы охлаждения генератора. Нагреваемый теплоноситель передает тепловую энергию в теплообменники, в результате чего происходит подогрев материала до необходимой температуры.
По сравнению со стандартными
установками Reactor эффективность нагрева
увеличивается на 25%. Работа системы
нагрева контролируется с помощью специального программного обеспечения,
позволяющего оперативно изменять температурный режим и четко контролировать
рабочий процесс. В интегрированной системе для работы со вспененными
материалами не требуется использование нагревателя ЛКМ, а для работы с
полимочевиной необходимо наличие нагревателя малой мощности, что позволяет
использовать более экономичный генератор.
Предварительные расчеты, подтвержденные производственными испытаниями, показали, что экономия топлива может достигать 50%. Новые модели дозаторов представляют собой полноценную систему, расходующую меньшее количество электроэнергии, имеющую улучшенную теплоемкость и обладающую совершенной системой управления, обеспечивающей высокую эффективность и производительность.
Особенности конструкцииСтандартный дозатор Reactor компании Graco используется совместно с: воздушным компрессором, генератором, системой дыхательного воздуха, подающими насосами и т.д. Так как подключение генератора к установке Reactor значительно усложняет конструкцию и способ работы системы дозирования, разработчикам пришлось направить основные усилия на создание системы, полностью отвечающей ожиданиям дистрибьюторов и потребителей. Инженеры компании Graco определили три основных критерия, которые необходимо учесть при создании системы дозирования: расход электроэнергии и сжатого воздуха, конструктивные параметры системы и удобство эксплуатации.
Расход электроэнергии и сжатого воздухаРасход электроэнергии и сжатого воздуха оказывает значительное влияние на работу установки Reactor. Разработчиками оборудования было четко определено, для каких элементов системы необходимо повысить эффективность использования потребляемой энергии. Энергия необходима для работы оборудования, входящего в состав передвижной системы дозирования (см. рис. 3):
- Электромотор установки Reactor и нагреватели ЛКМ.
- Воздушный компрессор.
- Осушитель воздуха
.
- Воздух для дыхания.
- Осветительные приборы.
- Ленточные нагреватели или нагревательные маты.
- Подогрев или кондиционирование воздуха.
Имеющиеся энергозатраты можно разделить на две группы: энергия, потребляемая основными элементами системы (1-4), и энергия, потребляемая дополнительным оборудованием (5-7). Сжатый воздух используется для работы следующих элементов системы:
- Подающих насосов.
- Мешалок.
- Распылителя.
- Воздух для дыхания.
В связи с тем, что энергия сжатого воздуха формируется за счет электрической энергии, разработчикам пришлось решить две задачи: сократить расход сжатого воздуха и расход электроэнергии, не оказывая влияние на функциональность системы.
Возможность сокращения энергозатрат оказывает влияние на выбор мощности двигателя и генератора, используемых для работы интегрированной системы Reactor. В результате анализа и оптимизации расхода воздуха было установлено, что для работы дыхательной системы высокого давления используется слишком большой объем воздуха. Разработчики приняли решение использовать дыхательную систему низкого давления с двумя масками. Для большинства используемых материалов была определена оптимальная скорость вращения мешалки, так как было установлено, что расход воздуха напрямую зависит от скорости вращения.
Был разработан способ ограничения объема воздуха, используемого для работы мешалки, что позволило защитить менее мощный воздушный компрессор от перегрузки. Основной целью оптимизации было сокращение расхода электроэнергии: сокращение расхода электроэнергии, потребляемой нагревателями ЛКМ или отказ от их использования за счет применения тепловой энергии, вырабатываемой двигателем. Еще одной задачей стало ограничение пиковых значений энергопотребления, вызванных циклической работой воздушного компрессора. Других вариантов сокращения электроэнергии найти не удалось. Вместо ленточных нагревателей ЛКМ было рекомендовано использовать маломощные нагревательные маты.
Конструктивные параметры системыВторой основной задачей, поставленной перед группой разработчиков, была оптимизация конструктивных параметров системы. Необходимо было сконструировать установку, которая смогла бы поместиться в автоприцеп, автофургон или на тележку с ящичным кузовом (см. рис. 4).
Непосредственное влияние на
решение данной задачи оказывали вес и габаритные размеры
установки. Зачастую, при комплектации подвижной системы, дистрибьюторы
устанавливают генератор в специально отведенном месте, что позволяет улучшить
вентиляцию двигателя и уменьшить уровень шума.
В новой интегрированной системе, предназначенной для установки в кузове автомобиля/автофургоне, отсутствуют какие-либо перегородки, так как менее мощный двигатель является менее шумным. В случае необходимости, между двигателем и дозатором может быть установлена дополнительная перегородка. Для правильного охлаждения двигателя необходимо проложить каналы, соединяющие стену автофургона с радиатором. Это позволяет уменьшить количество расходных материалов и значительно сократить время, затрачиваемое на построение системы.
Удобство эксплуатацииТретьей основной задачей стала возможность постоянного контроля и технического обслуживания системы. Система управления двигателем, дозатором и распределительным блоком расположены в удобном для доступа месте. Двигатель и дозатор расположены таким образом, что оператор может с легкостью провести ремонт и техническое обслуживание оборудования. К примеру, Y- образные сетчатые фильтры снабжены манометром и термометром и находятся на комфортной для доступа высоте. Расположение силовых кабелей дозатора и основных компонентов системы удобно организовано, что значительно упрощает ремонт и диагностику неисправностей. В данном случае также отсутствует необходимость использования автоматических выключателей для дополнительных элементов системы.
ПРЕИМУЩЕСТВА ИСПОЛЬЗОВАНИЯ НОВЫХ ТЕХНОЛОГИЙНовая серия дозаторов Reactor воплощает в себе новейшие технологии, разработанные для нанесения полимочевины и вспененных материалов. Основные изменения в конструкции системы: применение технологии регенерации, использование менее мощного дизель-генератора, усовершенствование программного обеспечения, используемого для контроля температуры и уровня давления, а также более удобный пользовательский интерфейс.
Сокращение расхода топлива за счет применения технологии регенерацииДизельные двигатели, как и любое другое оборудование, в основе работы которого лежит преобразование энергии, обладают довольно низким КПД. Как видно на рис. 5, только 30% выработанной энергии расходуется на выполнение механической работы. По причине малой эффективности работы генератора из этих 30% только 80% преобразуется в электроэнергию. Приблизительно 76% топливной энергии расходуется впустую. В данном случае применение технологии регенерации позволяет значительно повысить эффективность работы системы и сократить расход топлива.
Как было указано ранее, регенерация - процесс совместной выработки электрической и тепловой энергии одним источником энергии. Уменьшение расхода энергии позволило использовать генератор меньшей мощности, вырабатывающий достаточно энергии, необходимой для обеспечения электропитания и подачи сжатого воздуха. Выработанное генератором тепло передается в теплообменник и используется для подогрева материалов, распыляемых с помощью дозатора. Использование технологии регенерации позволяет при меньшем расходе топлива вырабатывать такое же количество энергии, что вырабатывается в случае использования обычного генератора (см. рис. 6).
Полезная информация: экономия топлива происходит за счет уменьшения расхода энергии, потребляемой нагревателями ЛКМ, а не за счет уменьшения мощности генератора. 22 кВт генератор, используемый в интегрированной системе, расходует меньше топлива, чем стандартный 20 кВт генератор, используемый для обычного дозатора Reactor. Расход топлива пропорционален механической нагрузке двигателя, а не его размеру.
В стандартных передвижных дозирующих системах тепло, выработанное радиатором двигателя, не используется для получения полезной энергии. Интегрированная система дозирования Reactor имеет огромное преимущество: в ней происходит преобразование выработанного тепла в полезную энергию, кроме того, для работы системы дозирования требуется меньшее количество энергии. Происходит уменьшение расхода топлива.
Поясним ранее приведенный пример: 22 кВт генератор нагружен на 25-50%, в то время как энергия, вырабатываемая 20 кВт генератором, также используется и нагревателями, что нагружает 20 кВт генератор почти на 100%. Тепловая энергия, которая обычно не используется, передается через три теплообменника и два контура охлаждения и применяется для подогрева материала. На рис. 7 видно, как выработанное тепло поступает из контура охлаждения двигателя в теплообменник 1, а затем, прередается во вторичный контур охлаждения. Полученное тепло сохраняется во вторичном контуре охлаждения до тех пор, пока установка Reactor не подаст сигнал, информирующий о необходимости подогрева материала. Кроме того, это позволяет предотвратить попадание материала в двигатель в результате поломки теплообменника. Во вторичном контуре расположены 3 клапана, используемые для передачи теплоносителя в теплообменники A и В. Работа клапанов регулируется с помощью специального программного обеспечения, что позволяет контролировать температуру распыляемого дозатором материала. Тепло, не используемое для подогрева материала, отводится из системы с помощью радиатора.
Необходимо отметить, что система теплообменников позволяет нагревать материал максимум до 60°C. В случае необходимости подогрева материала до более высоких температурных значений, необходимо использовать электрический бустерный нагреватель, использование которого позволит подогревать материал до 82°C.
Наиболее эффективная передача тепла осуществляется в случае значительной разницы температур материала и теплоносителя. Температура теплоносителя в контуре охлаждения двигателя обычно равна 94°C. В том случае, если температура материала равна 82°C, разница температур составит всего 11°C. При высоких скоростях потока материала небольшая разница температур может стать причиной медленной передачи тепла, в результате чего температура материала может стать меньше 82°C. Использование дополнительного 4 кВт бустерного нагревателя позволит обеспечить температурный режим, необходимый для распыления полимочевины. Несмотря на указанное ограничение, система позволяет нагревать материал до 56°C без использования бустерного нагревателя и до 78°C в случае его использования. Указанные температурные значения превышают температуру нагрева материала, возможную в случае использования стандартной модели дозатора Reactor.
Дополнительным преимуществом разделения температурных режимов является ограничение максимальной температура материала, попадающего в насосы дозатора (до 60°C), что позволяет увеличить срок службы уплотнений насоса. Использование данного метода позволяет обеспечить необходимый контроль температурного режима при более эффективном энергопотреблении.
Эффективность энергопотребления является не единственным преимуществом. По сравнению со стандартным 40 кВт генератором, новый генератор более компактный, легкий и менее шумный. В интегрированной системе Reactor используется дизельный двигатель Perkins (29 л.с.) и 22 кВт генератор Mecc Alte™
В таблице1 приведены сравнительные характеристики стандартного 40 кВт генератора и генератора, используемого в интегрированной системе Reactor.
Новая программируемая система управления обладает дополнительными функциональными возможностями. К примеру, усовершенствованная система контроля уровня давления позволяет минимизировать перепады давления при прохождении поршнем насоса мертвых точек, что обеспечивает сбалансированность статического и динамического давления, в результате чего достигается равномерность подачи материала.
Эффективность энергопотребления также была достигнута за счет использования электротурбины, установленной на радиаторе. Включение/выключение турбины осуществляется с помощью программируемой системы управления, что позволяет поддерживать оптимальную температуру двигателя и теплоносителя. Ранее, при прохождении теплоносителя через радиатор, часть тепловой энергии расходовалось впустую.
Помимо обеспечения более эффективной работы двигателя, система также позволяет сохранять выработанное двигателем тепло, которое в дальнейшем может быть использовано для нагрева материала до более высокой температуры.
Пользовательский интерфейсЭлектронное устройство управления, модуль Advanced Display Module (ADM), обладает большим набором возможностей и позволяет оператору с легкостью выполнять каждодневные задачи (Рис. 8). Блок управления ADM контролирует работу модулей управления насосной системы и системы нагрева, а также отслеживает температуру и уровень давления.
По сравнению с модулем,
используемым в стандартных установках Reactor, данный модуль генерирует
более точные сообщения об ошибках, что значительно облегчает поиск и
устранение неисправностей. При выборе сообщения об ошибке на экране
отображается порядок действий, необходимый для быстрого устранения
неисправности.
Наличие USB – интерфейса, а также возможность сбора статистической информации, позволяет производить анализ состояния системы и отслеживать расход материала. Система может одновременно отображать давление материала А и В, что позволяет сбалансировать давление при запуске системы и упрощает процесс поиска и устранения неисправностей.
Функция расчета уровня находящегося в бочке материала, основанного на подсчете количества тактов, позволяет автоматически прекращать работу дозатора в случае недостаточного количества материала. В блоке управления ADM установки имеется возможность хранения параметров (рецептов) материалов, удобное для пользователей, распыляющих разные материалы. Также существует возможность использования удаленного дисплея, позволяющего контролировать работу системы не отходя от распылителя.
ЗАКЛЮЧЕНИЕПо сравнению со стандартными подвижными системами распыления, интегрированные дозаторы Reactor имеют ряд преимуществ, обладая при этом аналогичной или лучшей функциональностью. Система имеет компактные размеры и полностью готова к эксплуатации. Установка оборудования значительно упрощена за счет того, что генератор, электрическая панель и распределительный блок установлены заранее.
В случае необходимости, дополнительно могут быть установлены компрессор и осушитель воздуха. Расходы конечного потребителя значительно снижаются за счет использования менее мощного двигателя, расходующего меньший объем топлива, а также использования выработанной тепловой энергии для подогрева материала А и В, позволяющего сократить расход электроэнергии. Для подсчета объема расходуемого топлива можно воспользоваться он-лайн калькулятором, учитывающим конфигурацию системы.
Использование Graco Fusion® 02 позволяет распылять материал, нагретый до 56°C (или 78°C в случае использования бустерного нагревателя) при изначальной температуре материала, равной 4°C. В обоих случаях подогрев материала происходит намного быстрее, чем в случае использования стандартных дозаторов Reactor. Наличие новых элементов управления и электронного дисплея облегчает управление системой, а также поиск и устранение неисправностей.
Помимо этого, существует возможность сохранения статистической информации на съемном носители, имеется функция определения объема материала, находящегося в бочке, а также функция сохранения настроек для определенного типа используемого материала, кроме того, возможна установка параметров автоматического выключения в случае неравномерности давления и недостаточного объема материала. Дополнительно можно использовать выносной дисплей, устанавливаемый рядом с распылителем. Усовершенствованная система контроля уровня давления позволяет обеспечить равномерность подачи материала. Значительно уменьшен перепад между статическим и динамическим давлением, а также снижено колебание давления при прохождении поршнем насоса мертвых точек. Все вышеперечисленные преимущества позволяют значительно сократить стоимость проводимых работ, что способствует повышению спроса на данное оборудование.
Применение интегрированной системы Reactor, работа которой основана на совместном использовании дозаторов Graco и технологии регенерации, позволяет значительно сократить временные и материальные затраты.
Остались вопросы?
Звоните +7 495 229-3095